Accident Investigations
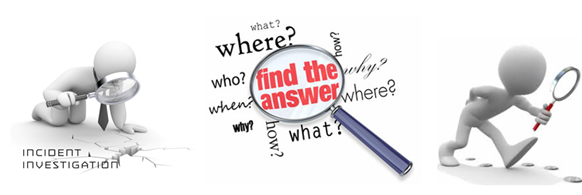
Accident Investigation Report Form - can be found here.
An investigation is an "after the fact" response. It is a process that uncovers hazards or problems that can be eliminated so similar events will not happen in the future.
The term "accident" can be defined as an unplanned event that interrupts the completion of an activity, and that may (or may not) include injury or property damage. An incident usually refers to an unexpected event that did not cause injury or damage this time but had the potential. "Near miss" or "dangerous occurrence" are also terms for an event that could have caused harm but did not.
Reasons for conducting a workplace accident investigation are:
- most importantly to find out the cause of accidents and to prevent similar accidents in the future;
- to fulfill the legal requirement;
- to determine the cost of an accident;
- to determine compliance with applicable safety regulations.
Incidents that involve no injury or property damage should still be investigated to determine the hazards that should be corrected. The same principles apply to a quick inquiry of a minor incident and to the more formal investigation of a serious event.
What Steps are Involved in Investigating an Accident?
The accident investigation process involves the following steps:
- Report the accident occurrence to a designated person within the organization
- Provide first aid and medical care to injured person(s) and prevent further injuries or damage
- Investigate the accident
- Identify the causes
- Report the findings
- Develop a plan for corrective action
- Implement the plan
- Evaluate the effectiveness of the corrective action
- Make changes for continuous improvement
As little time as possible should be lost between the moment of an accident or near miss and the beginning of the investigation. In this way, one is most likely to be able to observe the conditions as they were at the time, prevent disturbance of evidence and identify witnesses. The tools that members of the investigating team may need (pencil, paper, camera, film, camera flash, tape measure, etc.) should be immediately available so that no time is wasted.
Who Should Participate in the Accident Investigation?
Ideally, an investigation would be conducted by someone experienced in accident causation, experienced in investigative techniques, fully knowledgeable of the work processes, procedures, persons and industrial relations environment of a particular situation.
In Manitoba investigations must be conducted jointly, with both management and labour represented, or the investigators should be knowledgeable about the work processes involved. In most cases, the supervisor is the main investigator joined by one or more worker reps from the safety and health committee. Other members
of the team may include:
- employees with knowledge of the work
- safety officer
- health and safety committee
- union representative, if applicable
- employees with experience in investigations
- "outside" expert
- representative from local government
What Should be Looked at as the Cause of an Accident/Incident?
The causes of any accident can be grouped into five main categories - task, material, environment, personnel and management. When conducting your investigation each category should be looked at to determine the root cause of the accident/incident. The root cause may be one category or a combination of categories that all contributed to the accident/incident.
Task: Here the actual work procedure being used at the time of the accident is explored. Members of the accident investigation team will look for answers to questions such as:
- Was a safe work procedure used?
- Had conditions changed to make the normal procedure unsafe?
- Were the appropriate tools and materials available?
- Were they used?
- Were safety devices working properly?
- Was lockout used when necessary?
For most of these questions, an important follow-up question is "If not, why not?"
Material: To seek out possible causes resulting from the equipment and materials used, investigators might ask:
- Was there an equipment failure?
- What caused it to fail?
- Was the machinery poorly designed?
- Were hazardous substances involved?
- Were they clearly identified?
- Was a less hazardous alternative substance possible and available?
- Was the raw material substandard in some way?
- Should personal protective equipment (PPE) have been used?
- Was the PPE used?
- Were users of PPE properly trained?
Again, each time the answer reveals an unsafe condition, the investigator must ask why this situation was allowed to exist.
Environment: The physical environment, and especially sudden changes to that environment, are factors that need to be identified. The situation at the time of the accident is what is important, not what the "usual" conditions were. For example, accident investigators may want to know:
- What were the weather conditions?
- Was poor housekeeping a problem?
- Was it too hot or too cold?
- Was noise a problem?
- Was there adequate light?
- Were toxic or hazardous gases, dusts or fumes present?
Personnel: The physical and mental condition of those individuals directly involved in the event must be explored. The purpose for investigating the accident is not to establish blame against someone but the inquiry will not be complete unless personal characteristics are considered. Some factors will remain essentially constant while others may vary from day to day:
- Were workers experienced in the work being done?
- Had they been adequately trained?
- Can they physically do the work?
- What was the status of their health?
- Were they tired?
- Were they under stress (work or personal)?
Management: Management holds the legal responsibility for the safety of the workplace and therefore the role of supervisors and higher management and the role or presence of management systems must always be considered in an accident investigation. Failures of management systems are often found to be direct or indirect factors in accidents. Ask questions such as:
- Were safety rules communicated to and understood by all employees?
- Were written procedures and orientation available?
- Were they being enforced?
- Was there adequate supervision?
- Were workers trained to do the work?
- Had hazards been previously identified?
- Had procedures been developed to overcome them?
- Were unsafe conditions corrected?
- Was regular maintenance of equipment carried out?
- Were regular safety inspections carried out?
This type of accident investigations provides a guide for uncovering all possible causes and reduces the likelihood of looking at facts in isolation. Note: it should be emphasized that the above sample questions do not make up a complete checklist, but are examples only.
Please provide your question and email address in the fields below.
Your question has been successfully submitted.
CloseThank you.